Chemical resistant flexible heaters that work also highly efficient at high temperatures
- Koen Hollevoet
- Jun 25, 2020
- 2 min read
Updated: Jun 30, 2020
Flexible heater circuits are very suitable to apply local heating on surfaces that have very specific forms and curves (e.g. pipes, cylindric containers, bended structures, etc.). The applications are numerous across all industries (general industry, aerospace, defense, medical, oil& gas, etc.).
The conductor selection drives the resistance, hence impacts the power density. The primary function of the dielectric material is to be an electrical insulator, to prevent a short circuit between the heater circuit and other conducting parts. However, the dielectric material has also a very important impact on the durability and the efficiency of the heater.
Polyimide (yellow transparent ‘plastic’) and silicone rubber are typically used to encapsulate flexible heater circuits that need to operate in chemical challenging environments and/or in a wide temperature window. But these materials have also their limitations.

Chemical resistance
PEEK (Poly-Ether-Ether-Ketone) is a high-performance thermoplastic material that is basically chemically inert. This makes our XRL 2000 laminates extremely robust. Moisture, gasses, solvents, and other chemicals that may get in contact with this dielectric material will not affect the integrity of the heater circuit, nor cause any other chemical reactions.
Because of the absence of solvents in the PEEK material, there is also no outgassing. This is important when operating in vacuum or in sensitive atmospheres.
Health and Safety
Our XRL 2000 laminates are inherent flame retardant. They do not contain any halogens, and they cause no toxic fumes from the circuit material when exposed to a fire.
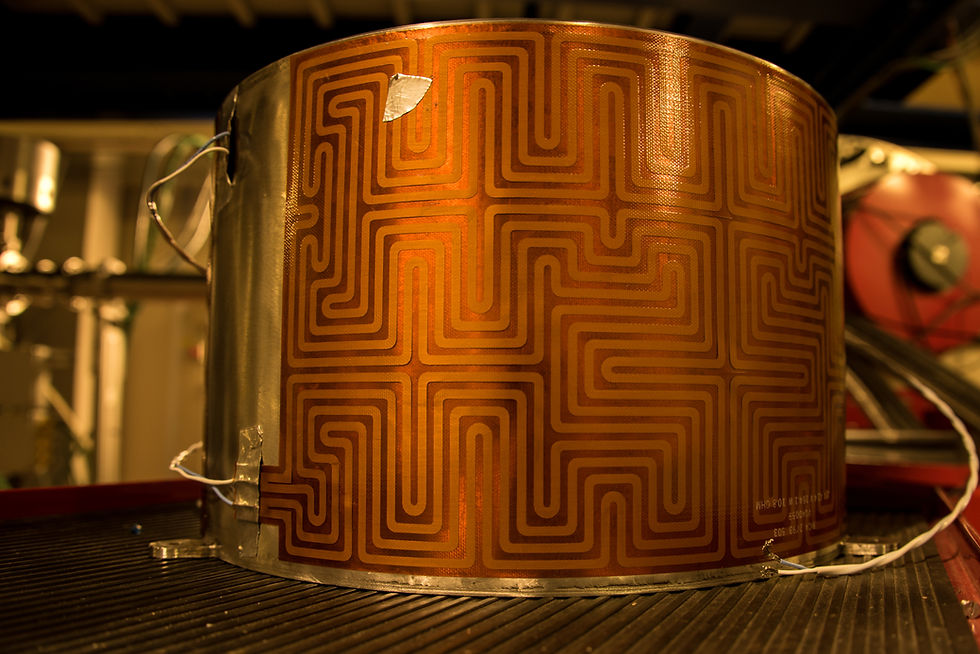
High temperature capability (>200°C/392°F)
The melting point of PEEK is 343°C (650°F). Tests confirmed great insulating performance when operating at high temperatures. After more than 100 days continuous operating at 260°C (500°F), and up to 300°C (572°F) in an inert environment, the laminate did not show any delamination nor any significant insulation resistance breakdown.
Numerous thermal shocks from room temperature to 288°C (550°F) (dip in liquid solder) and back, never showed any delamination or significant drop in adhesion between conductor and dielectric.
Great heating efficiency safes power
The purpose of a heater circuit is to heat up a target medium (solid, liquid or gas). This should be as efficient as possible to minimize power consumption, and to control the temperature as stable and direct as possible.
The standard cladding for XRL 2000 laminates is Copper, however various other metals (e.g. nickel, stainless steel, Inconel, etc.) are also possible to increase the power density of the heater circuit. Also multi-layer constructions are feasible.
XLR 2000 laminates are very thin (typically 50-100 µm range). The dielectric has a thermal conductivity of >0,3 W/mK? This is at least 50% better conductivity than the typical materials used in flexible heater circuits. Thinness and thermal conductivity enable a highly efficient heat transfer from the circuit to the target that needs to be heated.
Therefore, XLR 2000 laminates are an excellent choice for making durable and reliable flexible heater circuits that need to operate safely in chemical challenging environments, and/or need to operate highly efficient at high temperatures.
For more information, do not hesitate to contact Compolam (info@compolam.com).
Let us assist you to define the best fit laminate for your application.
תגובות